Versatile battery analysers from AMETEK Scientific Instruments are being put to use in applied R&D and production settings where they enable repeatable test sequences over extended time periods
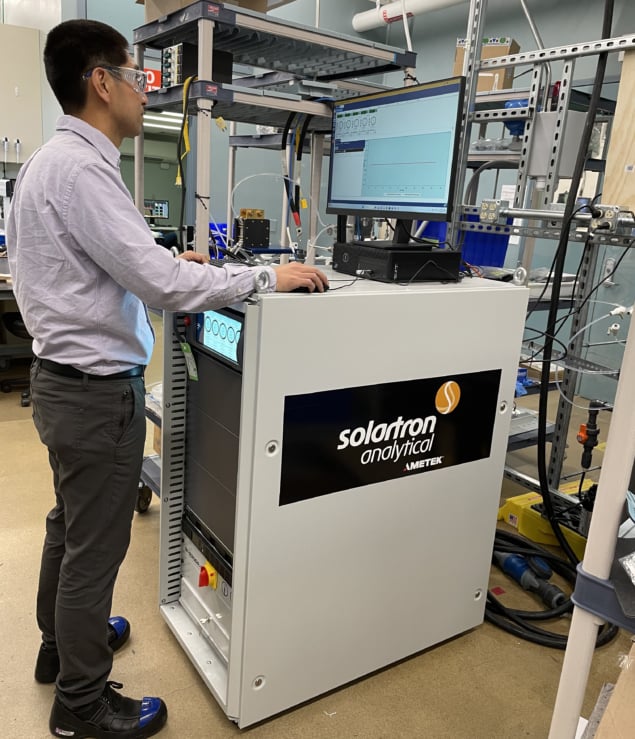
Cutting-edge technologies to cover all the bases versus cost, performance and innovation. That’s the mantra for the product development team at AMETEK Scientific Instruments (AMETEK SI), the US manufacturer of specialist test systems for electrochemical studies and battery characterization. Zoom in a bit and the operational reference points are similarly clear. Front-and-centre is a cosmopolitan customer mix – spanning academic research, industry R&D and volume manufacturing – plus a comprehensive electrochemical portfolio – battery cyclers, potentiostats, galvanostats, frequency response analysers, and plenty more in terms of ancillary hardware and software.
Alignment is all, with AMETEK SI end-users and products mapped synchronously across a diverse range of test and measurement applications – energy-storage systems, physical electrochemistry, corrosion science, biomedical devices and solid-state materials – and building upon a combined 100+ years of technology leadership across the manufacturer’s three core brands: Princeton Applied Research, Solartron Analytical and Signal Recovery.
Performance over time
If that’s the back story, what of the now and next on the development roadmap? Near term, the alignment of technology innovation with evolving end-user requirements underscores AMETEK SI’s latest product offerings: the SI-6200 and SI-9300R battery cyclers for research and production testing of advanced batteries destined for applications in mobile phones, PCs, electric vehicles (EVs) and the like. In brief, these high-performance battery cyclers enable researchers and manufacturers to compare the merits of novel battery chemistries and materials, with repeatable cycling tests running over extended time frames (several weeks to several months) to validate lifetime performance along multiple coordinates.
As such, AMETEK SI battery cyclers enable all manner of test capabilities: constant current, constant voltage (CC-CV); constant power (CP); constant resistance (CR); cyclic voltammetry (CV); as well as a range of fast-pulse and voltage/current ramp schemes. Advanced diagnostic modalities are also in the mix, including electrical impedance spectroscopy (EIS), a non-destructive technique for so-called “state-of-charge” (SOC) analysis and early fault detection inside the battery; urban-drive-profile cycle testing (arbitrary waveforms) to simulate the real-world environment experienced by battery cells in EV applications; and differential capacity analysis to track state-of-health (SOH) and structural changes in battery materials over repeated cycles of charge/discharge.
The SI-6200, for its part, is designed for testing next-generation battery materials, supercapacitors and micro fuel cells at up to 200 mA/10 V per channel. Among the analyser’s key features: stand-alone operation using stackable 10-channel modules (or cabinet-based); fast data acquisition speeds (thousands of measurements per second across all channels); and the incorporation of high-resolution 24-bit converters (to enable early detection of small differences in cell behaviours).
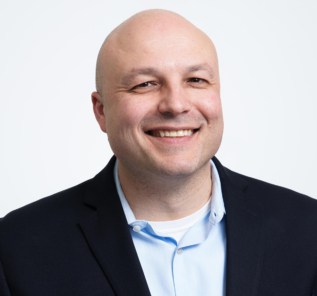
“Because of the relatively low current per channel, the SI-6200 is primarily focused on the testing of prototype coin cells and small-scale energy-storage devices,” explains Massimo DeSantis, Division Vice-President of AMETEK Advanced Measurement Technology (AMT), a broader business unit that includes AMETEK SI. “This initial-stage device development and testing represents the application ‘sweet spot’, though the cycler can be used in a production environment as well.”
Worth noting that the EIS capability, previously confined to academic research settings, is now transitioning to industrial R&D and production testing. It’s not hard to see why. For starters, EIS enables granular analysis of resistance, capacitance and impedance at different frequencies to track the electrical response of a battery. These frequency-dependent insights shed light on diverse performance issues – side reactions, electrode degradation, electrolyte ageing and SOH degradation among them.
What’s more, EIS is a non-invasive technique that can be used for in-situ or real-time monitoring without interrupting the battery’s normal mode of operation. That’s a big win and means manufacturers can deploy EIS measurements on batteries at different stages of production, ensuring consistency in performance and detecting any defects or anomalies early in the manufacturing process (when workflow efficiency and device reliability are of the essence).
Progressions of power
By extension, the SI-9300R battery cycler – the “big brother” of the SI-6200 – is designed for testing high-power batteries, fuel cells and electrolysers at up to 10 V/200 A. As such, each channel of the SI-9300R performs the same basic functions as the SI-6200 – with built-in EIS capability – though with additional features to target developers of EV batteries and so-called EV “second life” batteries (which have reached the end of their “automotive life” while retaining a residual capacity of about 70–80%).
Like its sister product, the SI-9300R is modular and scalable – with different cabinet options (42U and 24U) that can be controlled and monitored via multiple PCs – while as many as five channels can be connected in parallel to enable tests up to 1000 A. “We’re looking at applications in industrial R&D and indeed any research environment engaged in advanced prototype testing of high-power batteries and fuel cells,” notes DeSantis.
A key aspect of the SI-9300R is the implementation of regenerative power management which, according to the product team, can yield up to a 5x space saving and 90% saving in annual running costs over conventional battery cyclers. Without this sort of active intervention, there’s a lot of heat to be dissipated when the cells are discharging on multiple channels – and that means added real estate for cooling systems inside the analyser. In the SI-9300R, however, power is recirculated internally between channels that are simultaneously discharging and charging.
Meanwhile, system reliability is a major concern for end-users of battery-cycler equipment – the goal being truly autonomous cycling of those battery test sequences. With this in mind, both the SI-6200 and SI-9300R rely on AMETEK SI’s patented Direct-to-Disk technology to ensure a more secure, robust approach to data acquisition and storage. Put simply: data from the battery cycler is stored direct onto a disk drive – no intermediate PC – to minimize the risk of data loss.
All of which is reinforced by Aspire Energy Software – the “soul of AMETEK’s battery analysers” – which provides a fully integrated test environment for management of cyclers, climate chambers, data loggers and ancillary equipment. With product development teams often dispersed globally, Aspire’s shareable libraries enable tests, graphs and data analysis to be preconfigured and shared by all users to ensure consistency of results.
Operationally, it’s significant that AMETEK SI insists on deploying company-trained field engineers to support the installation, commissioning and acceptance of its battery cyclers in the customer’s lab or test facility. “Our motivations are clear,” concludes DeSantis. “It’s all about prioritizing a smoother onboarding process, faster resolution of technical queries, and a training programme that’s geared to deliver satisfied end-users every time.”