Research teams at Cranfield University in the UK are developing novel materials and processes in the quest for greener, more sustainable manufacturing
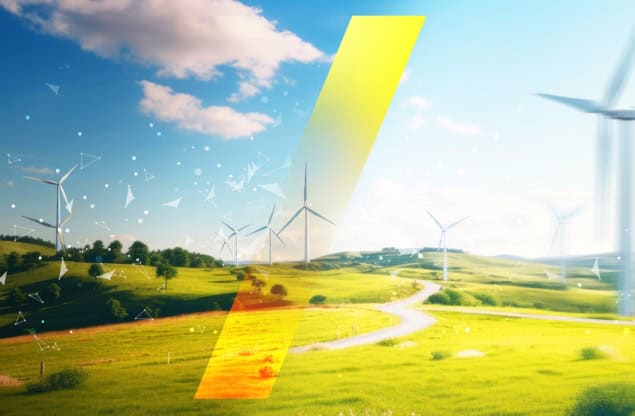
The manufacturing industry is one of the largest emitters of carbon dioxide and other greenhouse gases worldwide. Manufacturing inherently consumes large amounts of energy and raw materials, and while the sector still relies mainly on fossil fuels, it generates emissions that directly contribute to climate change and environmental pollution. To combat global warming and its potentially devastating impact upon our planet, there’s an urgent need for the manufacturing industry to move towards net zero operation.
Cranfield University, a specialist postgraduate university in the UK, is working to help the industry achieve this task. Teams at the university’s science, technology and engineering centres are devising ways to accelerate the journey towards more sustainable manufacturing – whether by introducing manufacturing processes that use less energy and raw materials; investigating renewable and low-carbon energy sources; creating new materials with enhanced recyclability; or implementing smart functions that extend the life of existing assets.
Greener manufacturing
One way to lower the carbon footprint of manufacturing is to move to 3D printing, an additive fabrication technique that inherently reduces waste.
“The machining techniques used in conventional manufacturing require a lot of power and a lot of raw material, which itself requires energy to create,” explains Muhammad Khan, acting head of Cranfield’s Centre for Life-cycle Engineering and Management and reader in damage mechanics. “In 3D printing, however, the amount of power required to generate the same complex part is far less, which impacts the overall carbon footprint.”
Materials used for 3D printing, particularly polymeric or other organic materials, are generally recyclable and easier to reuse, further reducing emissions. “Within our centre, we are working on polymeric materials to replace existing metallic materials in areas such as aerospace and automotive applications,” says Khan.
3D printing also enables manufacturers to rapidly tailor the design and properties of a product to meet changing requirements.
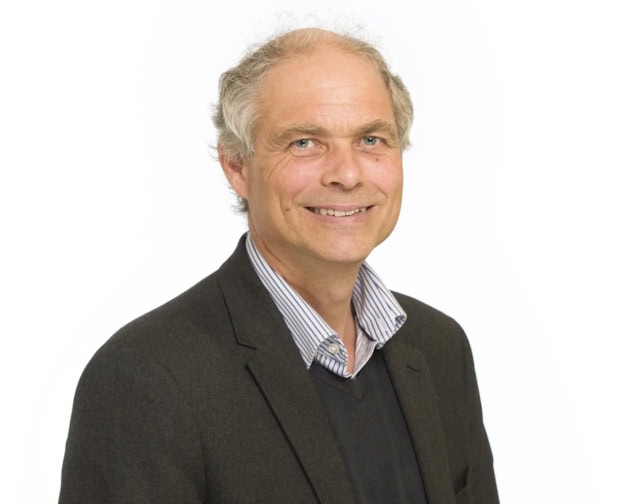
“We’ve seen this a lot in Formula One,” says David Ayre, a senior lecturer in composites and polymers in Cranfield University’s Composites and Advanced Materials Centre. “They’ll 3D print prototyping materials to quickly push out the structures they need on their cars. Twenty years ago, the resins used for this were brittle and only suitable for prototyping. But now we have developed more robust resins that can actually be used on working structures.”
Another benefit of 3D printing is that it can be performed on a smaller scale, enabling manufacturing sites to be installed locally. This could be next to the resource that the printer will use or next to the consumers that are going to use it; in either case, reducing transportation costs. While the cost implications of this “end of the street” model haven’t yet won through, the pressure to reduce CO2 emissions “might be the driver that starts to change the way we look at manufacturing”, Ayre notes.
Recycling opportunities
The introduction of novel advanced materials can also help increase sustainability. Thermal barrier coatings developed at Cranfield, for example, enable jet engines to work at higher temperatures, increasing efficiency and reducing fuel consumption. “There’s a huge role for engineers to play,” says Ayre.
Designing materials that can be recycled and reused is another important task for Ayre’s team. Producing raw material requires vast amounts of energy, a step that can be eliminated by recycling. Aluminium, for instance, is easy to process, highly recyclable and used to create a vast spectrum of products. But there are still some challenges to address, says Ayre.
“The aerospace industry likes to machine parts. They’ll take a one tonne billet of aluminium and end up with a 100 kg part,” he explains. “I worked with a student last year looking at how to recycle the swarf that comes from that machining. Unfortunately, aluminium is quite reactive and the swarf oxidizes back to the ore state, where it’s not really easy to recycle. These are the sorts of issues that we need to get around.”
The centre also focuses on composite materials, such as those used to manufacture wind turbine blades. Ayre notes that turbine blades built in the 1970s are now reaching the end of their usable life – and the composites they’re made from are difficult to recycle. The team is working to find ways to recycle these materials, though Ayre points out that it was such composites that enabled growth in the wind turbine market and the resulting source of renewable energy.
Alongside, the researchers are developing recyclable composite materials, such as bioresins and fibres produced from natural products, although work is still at an early stage. “These materials don’t have the same properties as petroleum-derived resins and ceramic, carbon and glass fibres,” Ayre says. “I don’t think we’re close yet to being able to replace our super-lightweight, super-stiff carbon fibre composite structures that motorsport and aerospace are utilizing.”
Smart materials
Meanwhile, Khan’s team at Cranfield is developing materials with smart functionalities, such as self-healing, self-cleaning or integrated sensing. One project involves replacing domestic pipelines used for wastewater distribution with 3D-printed self-cleaning structures. This will reduce water requirements compared with conventional pipelines, reducing the overall carbon footprint.
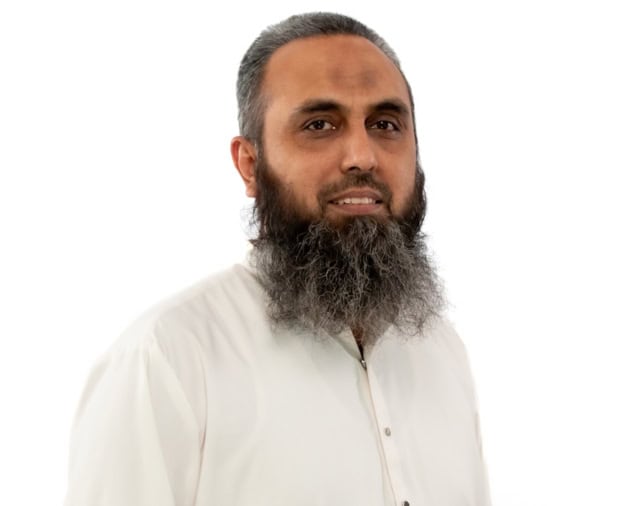
With a focus on maintaining existing assets, rather than creating new ones, the researchers are also developing self-healing structures that can repair themselves after any damage. “If you can extend device life twice or thrice by utilizing these smart mechanisms, you can reduce the amount of raw material used and the emissions generated during manufacturing of replacement parts,” says Khan. “This can positively contribute to the net zero agenda.”
Another project involves developing structures with integrated sensing functionality. Such devices, which monitor their own health by providing information such as displacement or vibration responses, eliminate the need to employ external sensors that require energy to construct and operate. The diagnostic data could provide users with an early warning of signs of damage or help determine the remaining useful life of a structure.
“Life estimation is challenging, but is something we are looking to incorporate in the future – how we can utilize the raw data from embedded sensing elements to model the remaining useful life,” says Khan. “That prediction could allow users to plan maintenance and replacement routines, and save a system from catastrophic failure.”
Building for the future
Cranfield University also aims to embed this sense of sustainability in its students – the engineers of the future – with a focus on net zero integral to all its engineering and related courses.
“The majority of our manufacturing and materials students will go on to an engineering career and need to appreciate their role in sourcing sustainable materials for any parts they’re designing and investigating manufacturing routes with low CO2 footprint,” Ayre explains. Students also learn about asset management – choosing the right product in the initial stages to minimize maintenance costs and extend a component’s life.
Elsewhere, Khan is working to ensure that standards agencies keep sustainability in mind. His centre is part of a consortium aiming to bring the goal of achieving net zero into standards. The team recently demonstrated how the existing asset management standard – ISO 15,000 – can be modified to incorporate net zero elements. The next step is to convince ISO and other agencies to accept these concepts, allowing people to manage their assets in a more environmentally friendly way without compromising availability or performance.
Ultimately, says Ayre, alongside “trying to encourage humanity not to want more and more and more”, lowering global emissions could rely on engineers getting creative and finding innovative ways to produce products that people want, but at reduced cost to the environment. It’s also vital that customers take on these ideas. “There’s no point us coming up with new-fangled manufacturing process and new materials if nobody has the experience or the confidence to take it anywhere,” he points out.
“It’s important that everyone makes a move towards net zero, because we’re not going to make any impact unless the whole world is on board,” says Ayre.